A racking inspection is crucial to maintain a safe and efficient workspace, but it is something that can be easily overlooked. Without regular inspections, warehouse racking can pose serious safety hazards, leading to injury and inventory damage. That’s why inspection consultations are crucial for any business that usesĀ warehouse racking.
The Rack Group has written this piece to discuss what makes an effective racking inspection, why it matters, regulations, and how it can benefit your business. So, whether you’re looking to undertake your own inspections or want to understand how to choose a third-party inspection service, keep reading for our expert insights.
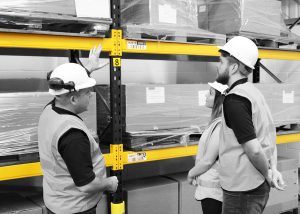
Understanding SEMA and why it matters for warehouse inspections
For warehouse racking inspections one organisation stands out as a recognized authority on safety and quality: the Storage Equipment Manufacturers’ Association, or SEMA.
SEMA is a UK-based trade organization that represents manufacturers and suppliers of storage equipment, including racking and shelving systems.
So why does SEMA matter when it comes to inspections? For one, SEMA-approved inspectors have access to the latest industry knowledge and adhere to strict safety standards, ensuring that their inspections are thorough, accurate, and effective. In the eyes of HSE it makes them the ‘Technically Competentā person who might be a trained specialist within an organisation, a specialist from a racking supplier, or an independent qualified rack inspector.
If you’re looking for an effective racking inspection, we highly recommend choosing a SEMA-approved inspector, to have confidence in the safety and quality of your warehouse racking.
The importance of HSE guidelines for warehouse inspections
Another crucial factor when choosing a racking inspector is adherence to HSE (Health and Safety Executive) guidelines for warehouse safety and inspections. HSE is the UK government agency responsible for promoting and enforcing workplace safety, including warehouse operations.
Following HSE guidelines for racking inspections can have numerous benefits for businesses. For one, it helps businesses maintain compliance with government regulations, avoiding potential fines and penalties as well as injury and fatalities!
Following HSE guidelines helps with record-keeping and documentation, which can be crucial in the event of an accident or liability claim.
When choosing a racking inspector, it’s important to ensure that they are accredited and follow HSE guidelines for safety and inspections. Familiarising yourself with these guidelines can also help you identify potential safety hazards and ensure that your warehouse is as safe as possible.
What to expect from a racking inspection and inspector
Inspections are designed to help prolong the lifespan of your racking systems by identifying any signs of wear and tear or damage that could compromise safety or performance. Addressing these issues early, it can help you avoid costly repairs or replacements down the line.
In addition to the cost savings associated with identifying potential risks early, inspections can also help you reduce liability and claims. By ensuring that your racking systems are safe and compliant with the latest health and safety legislation, you can protect your business from costly claims and legal fees.
An inspection process begins with a visual inspection of your storage systems, during which the inspector will look for any signs of damage, wear, and tear if it meets with the original manufactures design and build standards, or other issues that could compromise safety. They will also check that your systems are in compliance with the latest health and safety legislation, including HSE regulations.
Once completed the inspector should provide you with a detailed report outlining any issues identified and recommendations for how to address them using the SEMA/PUWER/EN15635 Red, Amber, and Green classifications. Sometimes this report can be overwhelming or confusing, which is why a good inspector will take the time to walk you through any identified situations in the report. The inspector should want to ensure that you have all the information you need to make informed decisions about how to address any issues and ensure the safety and compliance of your storage systems.
According to SEMA, after an annual racking inspection, a warehouse racking inspector should provide the following:
Detailed report:Ā The inspector should provide a detailed report outlining the findings of the inspection. The report should include a description of any damage or defects found in the racking system, as well as recommendations for repairs or replacements.
Risk assessment:Ā The inspector should provide a risk assessment that evaluates the safety of the racking system. The risk assessment should identify any potential hazards or risks associated with the racking system and recommend measures to mitigate those risks.
- SEMA’s RAG classifications are used to assess the severity of damage or defects found during a racking inspection. Here’s a breakdown of the classifications and their corresponding Priority rated actions:
- RED RISK – Areas where a high level of damage is identified of over twice the SEMA limits. This warrants immediate offloading and isolation of the affected area until repair work is carried out
- AMBER RISK – Areas where the damage identified is greater than the SEMA limits. This warrants remedial work to be carried out. However, the damage is not sufficiently severe to warrant the immediate offloading of the area. No additional loads shall be placed in the affected area and, once the pallet positions in this area are emptied, they should not be refilled until the repairs are carried out. If repairs are not carried out within 4 weeks, an Amber risk item automatically becomes a Red risk item
- GREEN RISK – Areas where damage is present, however, the level of damage is within the SEMA limits and should be recorded for further consideration at the next inspection
By using the RAG classifications and corresponding Priority rated actions, it aims to help you and racking inspectors prioritize and address any safety issues identified during an annual racking inspection. This ensures that any urgent risks are addressed immediately and that less urgent issues are addressed in a timely manner, reducing the risk of accidents and maintaining a safe working environment.
A good inspection company should go beyond just the inspection process and identifying issues, to provide support throughout the inspection process and beyond. Any inspectorās goal is to help you create a safer and more efficient warehouse environment that can help you reduce or eliminate repetitive damage, claims, and liability.
How to choose a racking inspection provider
Now that we’ve discussed the importance of racking inspections and what makes an effective inspector, how do you go about choosing a racking inspection provider? Here are some key factors to consider:
- Experience: Look for an inspector or provider with a proven track record of conducting effective and thorough inspections. Ask about their experience working with businesses similar to yours and ask for references if necessary.
- Qualifications: In addition to experience, look for a provider with relevant qualifications and certifications. For example, inspectors who are members of SEMA (Storage Equipment Manufacturers’ Association) are held to high standards of safety and quality.
- Reputation: Do some research on potential providers to see what their reputation is like in the industry. Look for reviews and testimonials from previous clients and ask for references if necessary.
- Cost: Of course, cost is an important factor to consider as well. However, don’t make cost your only consideration when choosing a provider. Remember that investing in a quality inspection can save you money in the long run by reducing the risk of accidents and associated costs.
When choosing a racking inspection provider, it’s important to take the time to research potential options carefully. Don’t be afraid to ask questions and seek out references to ensure that you’re making an informed decision based on your needs and budget. By choosing a qualified and safety-conscious provider, you can protect your employees, inventory, and bottom line.
When should I have racking inspected?
The frequency of pallet racking inspections required depends on a variety of factors that are particular to your site but, typically, the first inspection should be carried out within 6 months of the installation becoming operational and at least annually from then on.
PUWER is a set of regulations that apply to work equipment, including racking systems used in warehouses. The regulations require that all work equipment, including racking systems, has not deteriorated through use.
Under PUWER, warehouse racking systems must be inspected at regular intervals to ensure they remain safe for use. The frequency of inspections will depend on a number of factors, including the type of racking system, number of pallet movements, age of the system, previous damage recorded, type of system even new FLT operators and the level of risk associated with the racking system.
Finding an inspection partner with industry experience and commitment to cost savings!
At Rack Group, our inspectors donāt just identify issues but work with our clients to help address and stop issues from reoccurring.
We’re proud to draw on our 40 years of experience in the racking industry and to provide top-quality inspection services that help our clients save money and reduce risk. We’ve seen it all when it comes to racking systems, and our experience enables us to identify potential risks and issues before they become costly problems.
Our experienced qualified inspectors will walk you around any identified situations in the report, to spend the time to assist you with the information you need to ensure your storage systems are safe and compliant with the latest health and safety legislation. A large part of what we do is guidance on how and why issues occur, the action required to rectify them, and more importantly the actions needed to stop them from reoccurring. This further helps reduce risk and prolong the lifespan of your rackingā¦ultimately saving you money!
On completion of our electronic inspection from our PUWER and SEMA accredited team you will have a clear and concise digital next day report, highlighting;
- Priority-rated actions to SEMAās Red, Amber, and Green classifications
- Recommendations that will prolong the life of your storage equipment
- Guidance to improve workforce safety such as housekeeping
Our services go that extra mile to provide a comprehensive, friendly, and tailored service which has seen us become the pallet racking inspection company of choice, for many recognisable names within the UK and Ireland.
Our commitment to cost savings and risk reduction is just one of the many reasons why businesses trust us to provide top-quality inspection services. If you’re interested in learning more about how we can help you save money and reduce risk, please don’t hesitate to contact us to schedule an inspection. The Rack Group looks forward to working with you.
If you have any questions about our services or products,Ā please contact The Rack GroupĀ over the phone at +44 (0)1226 784488 or email via info@therackgroup.com.Ā