The official best practice for safety barriers and traffic management in industrial facilities
PAS 13 Code of Practice for Safety Barriers was developed by the British Standards Institution (BSI), and is published as the Publicly Available Specification (PAS) 13, Code of practice for safety barriers used in traffic management within workplace environments with test methods for safety barrier impact resilience.
What is PAS 13 code of practice?
PAS 13 is the only code of practice for industrial safety barriers that is recognised globally. It is intended to be used as a reference for engineers, architects, contractors, health and safety professionals, and other stakeholders involved in the design, construction, deployment and maintenance of safety barriers. The code is based on the principles of risk assessment and recommends selecting the appropriate safety barriers based on the potential hazards and risks.
Compliance with PAS 13 can help ensure that safety barriers are effective in protecting people and assets from potential hazards and minimize the risk of accidents and injuries.
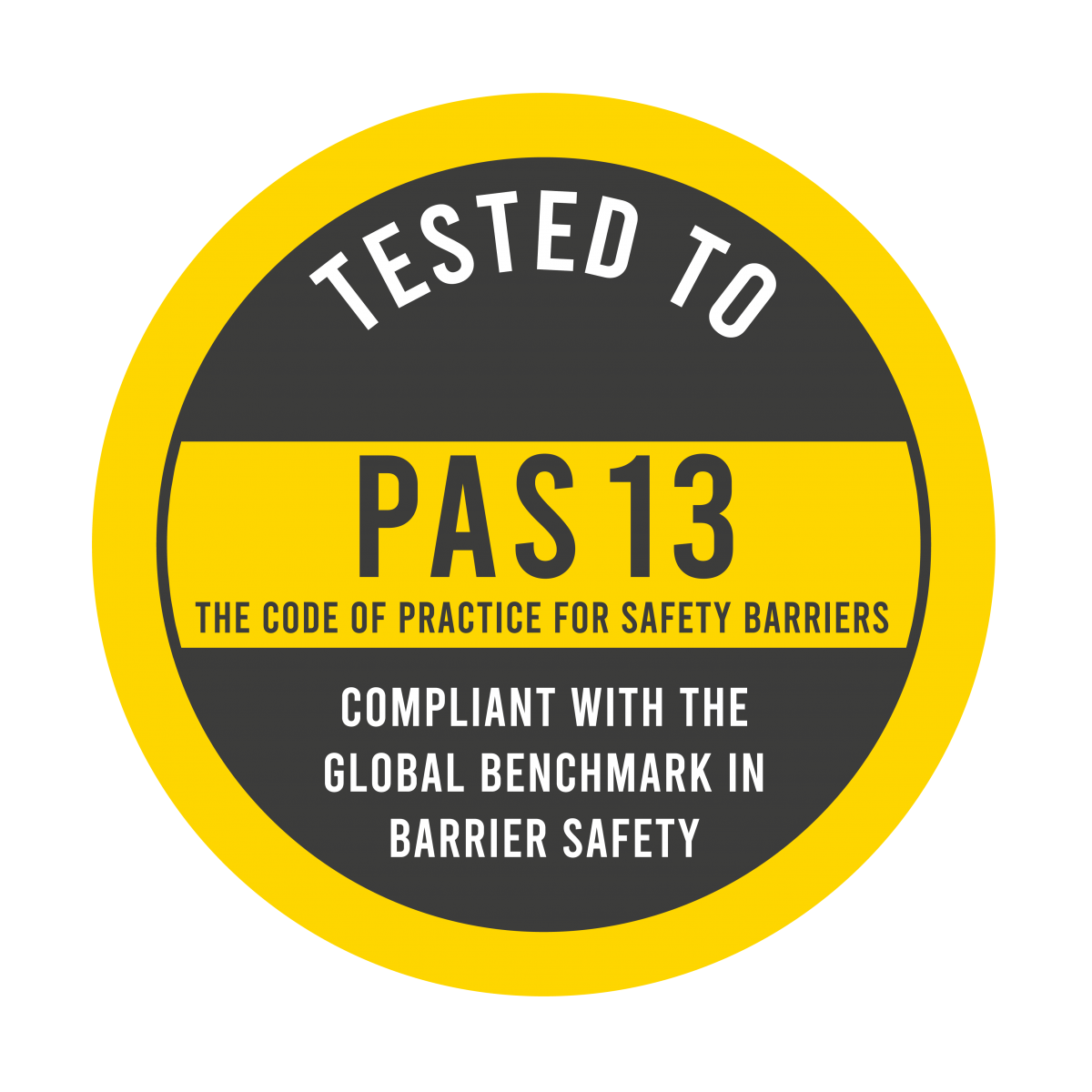
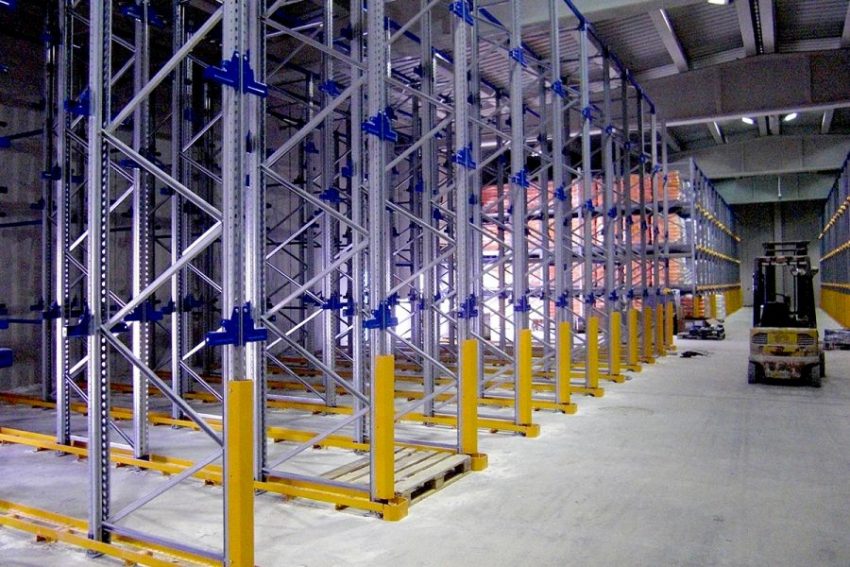
Why was PAS 13 created?
The consequences of workplace accidents and injuries can be severe. They can result in lost productivity, downtime, and increased maintenance and repair costs. Moreover, they can lead to long-term health problems for employees and even legal and financial liabilities for the company.
According to Health and Safety Executive statistics approximately 50 people are killed each year, and more than 5,000 injured, in accidents involving workplace transport. PAS 13 outlines the current good practice traffic management procedures for a workplace and provides a standard for the safety barriers within them.
Mixing vehicles and pedestrians increases the risk of potential accidents, so it is imperative that steps are taken to minimize the associated risks. PAS 13 gives recommendations for impact resilience, dimensions and positions of safety barriers in the workplace; guidance on how to manage the risks associated with vehicles within the workplace; and specifies the criteria for testing the impact resilience of a barrier.
Who created PAS 13?
PAS 13 was created and published by the British Standards Institution in association with the Health and Safety Executive. The BSI worked with a steering group made up of many high-profile blue-chip companies. These companies were able to offer first-hand experience of safety across a range of industries, to create a consistent and transferable set of guidelines for barrier installation.
Overview of PAS 13
PAS 13 is a code of practice for industrial safety barriers that provides comprehensive guidance on good practice for using industrial safety barriers. As mentioned earlier, it is an official document produced by the British Standards Institution (BSI) and is globally recognised as the most reliable code of practice for industrial safety barriers.
PAS 13 is broken down into two sections. The first section provides Health and Safety and Operations managers with detailed guidance on the correct application of safety barriers at busy industrial facilities. This section includes recommendations on how to select the appropriate barrier system based on the level of risk, traffic flow, and environmental conditions.
The second section of PAS 13 is primarily for safety barrier manufacturers. It covers how to conduct standardised testing of safety barriers for strength and durability and record results in a way that is clear and transparent for customers. This section of PAS 13 helps manufacturers ensure that their products meet the required strength and durability standards, giving customers peace of mind when selecting their barrier systems.
Advantages of using impact barriers in industrial workplaces
The use of impact barriers in industrial workplaces can have numerous benefits, including:
Racking protection
Impact barriers can also provide protection for racking and other storage systems. In busy industrial facilities, forklifts and other vehicles can cause damage to racking, which can be costly to repair or replace. Impact barriers can absorb the force of collisions, minimizing damage and reducing maintenance and repair costs.
Pedestrian protection
Impact barriers can be used to create safe pedestrian walkways in busy industrial facilities. By separating pedestrian areas from areas where vehicles are operating, the risk of accidents is greatly reduced. This can help to create a safer working environment and reduce the risk of accidents.
Forklift damage
Forklifts are a common cause of damage in industrial facilities, and collisions with other vehicles, racking, and equipment can be costly to repair. Impact barriers can help to absorb the force of collisions, reducing the risk of damage to forklifts and other vehicles.
Maintenance and repair costs
By reducing the risk of damage to racking, equipment, and vehicles, impact barriers can also help to reduce maintenance and repair costs. In addition, impact barriers themselves are designed to be durable and long-lasting, reducing the need for frequent replacement.
Employee safety
One of the most significant benefits of using impact barriers is the increased safety of employees. Impact barriers are designed to protect employees from accidents caused by moving machinery, falling objects, and collisions with vehicles. By providing a physical barrier between employees and potential hazards, the risk of injury is greatly reduced.
The use of impact barriers in industrial workplaces can have numerous benefits, including increased employee safety, protection for racking and other storage systems, safe pedestrian walkways, reduced damage to forklifts and other vehicles, and lower maintenance and repair costs. By investing in impact barriers and following the guidelines set out in PAS 13, companies can create a safer working environment and improve the efficiency of their operations.
PAS 13 benefitsĀ
Health and safety managers, procurement specialists, directors, facility managers, project managers and site safety leaders will benefit from PAS 13. It will also likely be of interest to those who want to apply traffic management procedures and those who test and measure the performance of safety barriers will also benefit from PAS, and manufacturers and distributors of safety barriers.
Here are some of the ways Implementing PAS 13 can greatly improve the use of impact barriers in industrial workplaces:
- Clear guidelines for barrier selection: PAS 13 provides detailed guidelines for the correct application of safety barriers in industrial facilities. This includes information on the selection of barriers that best fit the needs of the facility, taking into account factors such as vehicle types, traffic flow, and the potential for impact.
- Standardised testing for barrier strength and durability: The second section of PAS 13 covers how to conduct standardised testing of safety barriers for strength and durability, and record results in a way that is clear and transparent for customers. This ensures that all barriers used in the facility meet a consistent standard for safety and durability.
- Improved traffic management: The guidelines set out in PAS 13 can also help to improve traffic management in industrial facilities. By using barriers to separate pedestrian walkways from areas where vehicles are operating, the risk of accidents is greatly reduced. This can help to create a safer working environment and improve the efficiency of operations by reducing downtime due to accidents.
- Safety: The primary objective of impact barriers is to prevent accidents and protect workers from hazards. By manufacturers following the recommendations and requirements set out in PAS 13, customers can ensure that their safety barriers are properly designed and installed to provide maximum protection for workers.
- Risk assessment: PAS 13 emphasises the importance of conducting a thorough risk assessment before installing safety barriers. This helps businesses identify potential hazards and ensure that their safety barriers are designed to address these specific risks.
- Cost-effectiveness: Properly designed and installed safety barriers can help reduce the risk of accidents and damage to equipment and products, which can ultimately result in cost savings for businesses.
In conclusion, the use of impact barriers in industrial workplaces is essential for protecting employees and equipment from harm. The implementation of the PAS 13 code of conduct for industrial safety barriers provides a reliable and effective means of ensuring that the correct barriers are selected and used in the workplace. PAS 13 provides clear guidelines for barrier selection, standardised testing for barrier strength and durability, improved traffic management, reduced maintenance and repair costs, and compliance with safety regulations.
By following the guidelines set out in PAS 13, companies can create a safer working environment and improve the efficiency of their operations. Investing in high-quality impact barriers that meet PAS 13 standards not only reduces the risk of accidents but also protects the company from liability and reduces maintenance and repair costs over time.
Therefore, we highly recommend that all industrial workplaces use the PAS 13 code of conduct when selecting and implementing impact barriers. As a leading provider of impact protection barriers, our company offers a range of high-quality barriers that meet PAS 13 guidance.
Contact us today to learn more about how we can help you improve safety in your industrial workplace and view our range of barriers.