Racking stock update
Rack Group now stock large quantities of the top racking manufacturers including:
- AR Racking
- Link 51
- PSS
- Cornix
- Dexion
Pre-order full bays or individual components, available with installation or supply only.
Get in touch with our team today for more information.
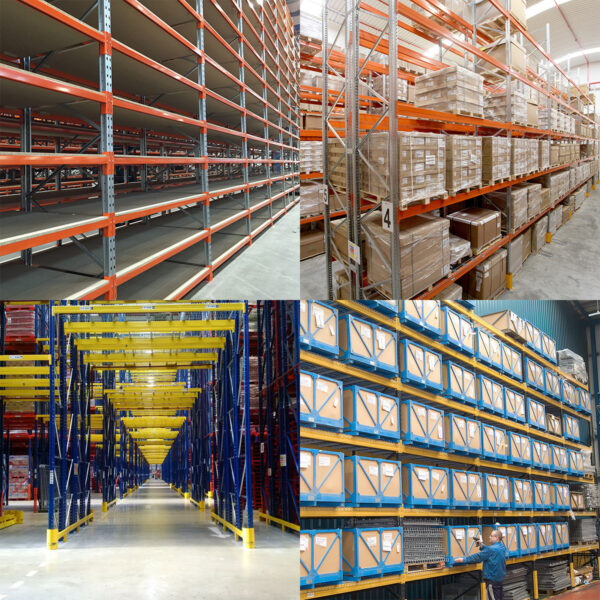
Link 51
We have Link 51 racking IN STOCK ready to be shipped. There is currently a 13 week lead time direct from the manufacturer, but Rack Group can deliver the following components NEXT DAY.
Current stock includes:
- Shelving - available assembled or in kit
- 2400 x 300
- 2400 x 500
- 2400 x 600
APR PALLET RACKING - available assembled or in kit
- Uprights
- 900 E / S
- 1350 E / S
- 2250 E / H / M / S
- 4500 H
- 5250 H
- 6450 H
- Beams
- 2700 x 105
- 2650 x 120
- 2670 x 120
- 2700 x 120
Cornix
Current stock includes:
- Frames
- 6300 x 900 M
- 3900 x 900 M
- 8400 x 900 M
- 9600 x 900 M
- Beams
- 2700 x 110
- Baseplates
- S/M/H
PSS
Current stock includes:
- Beams
- 2700 x 110
- 2250 x 100
- Ā Uprights
- 4050 2KL85 3.0L
- 4650 2KL85 3.0L
- 5250 2KL85 3.0L
- Bracing
- 787HC / 827OL PG
- 907HC / 947OL PG
- 1048HC / 1188OL
AR Racking
Current stock includes:
- Frames
- 6000 x 900 XS20
- 8500 x 900 M
- Beams
- 2700 x 110 2000kg
- 2700 x 150 3000kg
Subscribe to our news
Don't miss out on all the latest industry news and special offers from Rack Group! Sign up now to receive these direct to your email inbox.